無(wú)錫不銹鋼板、無(wú)錫不銹鋼管廠家無(wú)錫漢能不銹鋼2020年10月26日訊 高強(qiáng)度不銹鋼作為強(qiáng)度、韌性及服役安全性俱佳的金屬結(jié)構(gòu)材料,廣泛應(yīng)用于航空、航天及海洋工程等領(lǐng)域。本文系統(tǒng)地梳理了高強(qiáng)度不銹鋼的研究及發(fā)展歷程,重點(diǎn)闡述了以析出強(qiáng)化和奧氏體韌化為代表的強(qiáng)韌化機(jī)理,及以氫致開裂和H原子擴(kuò)散富集為主要因素的應(yīng)力腐蝕及氫脆敏感性問(wèn)題。認(rèn)為高強(qiáng)度不銹鋼的未來(lái)發(fā)展將重點(diǎn)關(guān)注計(jì)算模擬設(shè)計(jì),多類型、高共格度析出相復(fù)合強(qiáng)化,高機(jī)械穩(wěn)定性的薄膜狀?yuàn)W氏體韌化,綜合顯微組織和服役環(huán)境加深對(duì)應(yīng)力腐蝕及氫脆機(jī)理的理解,從而為設(shè)計(jì)兼?zhèn)涑邚?qiáng)韌性、優(yōu)良綜合服役性能的高強(qiáng)不銹鋼提供實(shí)際的理論依據(jù)。
關(guān)鍵詞: 超高強(qiáng)度不銹鋼 ; 強(qiáng)韌化機(jī)理 ; 氫脆 ; 應(yīng)力腐蝕 ; 析出相 ; 逆轉(zhuǎn)變奧氏體
高強(qiáng)度不銹鋼因其具有優(yōu)異的強(qiáng)韌性匹配及耐蝕性,在航空航天、海洋工程及能源等關(guān)系國(guó)計(jì)民生的裝備制造領(lǐng)域得到廣泛的應(yīng)用,如飛機(jī)的主承力構(gòu)件[1]、緊固件、衛(wèi)星陀螺儀、飛船外殼、海洋石油平臺(tái)、汽車工業(yè)、核能工業(yè)、齒輪和軸承制造等,是未來(lái)裝備部件輕量化設(shè)計(jì)和節(jié)能減排的首選材料。作為承力、耐蝕結(jié)構(gòu)件的重要候選材料之一,如何兼顧超高強(qiáng)韌性及優(yōu)良的服役安全性是此類鋼種未來(lái)的重點(diǎn)發(fā)展方向[2,3]。
為了滿足航空航天、海洋工程對(duì)高性能耐蝕結(jié)構(gòu)鋼的需求,美國(guó)CarnegieIllionois鋼鐵公司于1946年成功研發(fā)了第一代馬氏體沉淀硬化不銹鋼——Stainless W。在Stainless W鋼合金體系的基礎(chǔ)上,通過(guò)加入Cu、Nb元素并去除Al、Ti元素。美國(guó)Armco鋼鐵公司于1948年開發(fā)了17-4PH鋼[4],因其良好的強(qiáng)韌性及耐蝕性,除應(yīng)用于F-15飛機(jī)起落架構(gòu)件外,目前亦廣泛應(yīng)用于制造緊固件及發(fā)動(dòng)機(jī)零部件,但其冷變形能力較差。為了減少對(duì)橫向力學(xué)性能不利的高溫δ-鐵素體,通過(guò)降低鐵素體形成元素Cr的含量并增加Ni元素含量,研發(fā)出了15-5PH鋼[5,6,7],該鋼克服了17-4PH鋼橫向塑韌性差的缺點(diǎn),現(xiàn)已應(yīng)用于制造艦船及民用飛機(jī)等承力部件。20世紀(jì)60年代初,國(guó)際鎳公司發(fā)明了馬氏體時(shí)效鋼,為發(fā)展高強(qiáng)度不銹鋼引入了馬氏體時(shí)效強(qiáng)化這一概念,從而拉開了馬氏體時(shí)效不銹鋼發(fā)展的帷幕。1961年美國(guó)Carpenter Technology公司首先研制了含Mo的馬氏體時(shí)效不銹鋼Custom450;此后,在1967和1973年先后研制了PyrometX-15、Pyromet X-12。在此期間,美國(guó)也先后研制了AM363、In736、PH13-8Mo、UnimarCR等;Martin等[8,9]則分別于1997年和2003年獲得了Custom465和Custom475鋼的發(fā)明專利,并應(yīng)用在民航飛機(jī)上。英國(guó)研發(fā)了FV448、520、520(B)、520(S)等高強(qiáng)度不銹鋼牌號(hào)。德國(guó)于1967、1971年研制了Ultrafort401、402等。前蘇聯(lián)除仿制和改進(jìn)美國(guó)鋼號(hào)外,還獨(dú)立研究了一系列新鋼種,常見(jiàn)的鋼有0Х15Н8Ю、0Х17Н5М3、1Х15Н4АМ3、07Х16Н6等以及Co含量較高的鋼號(hào),如00Х12К14Н5М5Т、00Х14К14Н4М3Т等。2002年美國(guó)QuesTek公司承擔(dān)美國(guó)國(guó)防部戰(zhàn)略環(huán)境研究與發(fā)展計(jì)劃(SERDP)污染防止項(xiàng)目,通過(guò)材料基因組計(jì)劃設(shè)計(jì)并開發(fā)了新型飛機(jī)起落架用超高強(qiáng)度不銹鋼Ferrium?S53[10],于2008年底發(fā)表公開AMS5922宇航標(biāo)準(zhǔn),F(xiàn)errium?S53強(qiáng)度約1930 MPa,斷裂韌度(KIC)達(dá)到55 MPa·m1/2以上,在2017年增編入美國(guó)的MMPDS主干材料手冊(cè)中,該材料已經(jīng)成功應(yīng)用于美國(guó)的A-10戰(zhàn)機(jī)及T-38飛機(jī),是下一代艦載機(jī)起落架的首選材料。
我國(guó)從20世紀(jì)70年代開始高強(qiáng)度不銹鋼的研制工作,典型牌號(hào)有00Cr13Ni8Mo2NbTi、00Cr12Ni8Cu2AlNb、00Cr10Ni10Mo2Ti1等10余種[11]。2002年鋼鐵研究總院設(shè)計(jì)并研制出一種新型的超高強(qiáng)韌性的不銹鋼材料,是我國(guó)自主研發(fā)并具有自主知識(shí)產(chǎn)權(quán)的Cr-Ni-Co-Mo合金體系的超高強(qiáng)度不銹鋼USS122G,其強(qiáng)度超過(guò)1900 MPa,KIC達(dá)到90 MPa·m1/2以上[12]。目前該材料已經(jīng)突破了直徑300 mm大規(guī)格棒材制備的相關(guān)關(guān)鍵技術(shù),在我國(guó)航空航天裝備制造領(lǐng)域具有廣泛的應(yīng)用前景。
2、超高強(qiáng)度不銹鋼的研究現(xiàn)狀超高強(qiáng)度不銹鋼良好的綜合服役性能主要包括超高強(qiáng)度、優(yōu)良的塑性及韌性,與傳統(tǒng)低合金高強(qiáng)鋼及二次硬化型超高強(qiáng)度鋼相比,除具備優(yōu)良的綜合力學(xué)性能以外,還具有優(yōu)異的耐腐蝕、抗應(yīng)力腐蝕及腐蝕疲勞性能。為了提高上述服役性能,揭示其背后的影響因素及機(jī)理,國(guó)內(nèi)外學(xué)者圍繞超高強(qiáng)度不銹鋼的強(qiáng)韌化機(jī)理、應(yīng)力腐蝕開裂以及氫脆行為進(jìn)行了廣泛研究。2.1 高強(qiáng)度不銹鋼中的合金設(shè)計(jì)及強(qiáng)化相超高強(qiáng)度不銹鋼的典型室溫組織包括:細(xì)小的板條馬氏體基體,適量的殘余(或逆轉(zhuǎn)變)奧氏體以及彌散分布的沉淀強(qiáng)化相。板條狀馬氏體由于其自身的高位錯(cuò)密度,具有很高的強(qiáng)度。亞穩(wěn)殘余(逆轉(zhuǎn)變)奧氏體可以緩解裂紋尖端的應(yīng)力集中從而提高材料韌性。時(shí)效處理過(guò)程中析出的納米級(jí)強(qiáng)化相可以進(jìn)一步提高鋼的強(qiáng)度,按照析出相的合金組成可將其分為3類,即碳化物(MC、M2C)、金屬間化合物(NiAl、Ni3Ti)以及元素富集相(ε相、α'相)等,在超高強(qiáng)度不銹鋼中,沉淀相的強(qiáng)化潛力取決于沉淀相的本質(zhì)及其尺寸、數(shù)密度、體積分?jǐn)?shù)及空間分布情況等。能否獲得最優(yōu)性能主要取決于對(duì)沉淀相析出行為的熱、動(dòng)力學(xué)特性的掌控,進(jìn)而指導(dǎo)合金成分的調(diào)控以及熱處理工藝的制定。典型超高強(qiáng)度不銹鋼的化學(xué)成分和力學(xué)性能見(jiàn)表1[13,14,15,16,17,18,19,20,21]和表2[13,14,15,16,17,18,19,20,21]。從表中可以看出,第一代超高強(qiáng)度不銹鋼(15-5PH、17-4PH)強(qiáng)度級(jí)別較低(1200~1400 MPa),此類鋼中的主要強(qiáng)化相為元素富集相,如ε-Cu相;第二代高強(qiáng)度不銹鋼(PH13-8Mo、Custom465)中,C含量普遍較低(不大于0.05%,質(zhì)量分?jǐn)?shù),下同),主要強(qiáng)化方式為NiAl和Ni3Ti等金屬間化合物強(qiáng)化;作為第三代高強(qiáng)度不銹鋼的典型代表Ferrium?S53鋼的誕生得益于材料基因數(shù)據(jù)和計(jì)算機(jī)技術(shù),將C的質(zhì)量分?jǐn)?shù)增加到0.21%,M2C型碳化物的二次硬化作用使材料性能得到大幅度提升,不同于Ferrium?S53鋼的合金設(shè)計(jì)理念,國(guó)產(chǎn)USS122G鋼采用了兩相復(fù)合強(qiáng)化體系,相比于Ferrium?S53鋼具有更佳的強(qiáng)韌性匹配。
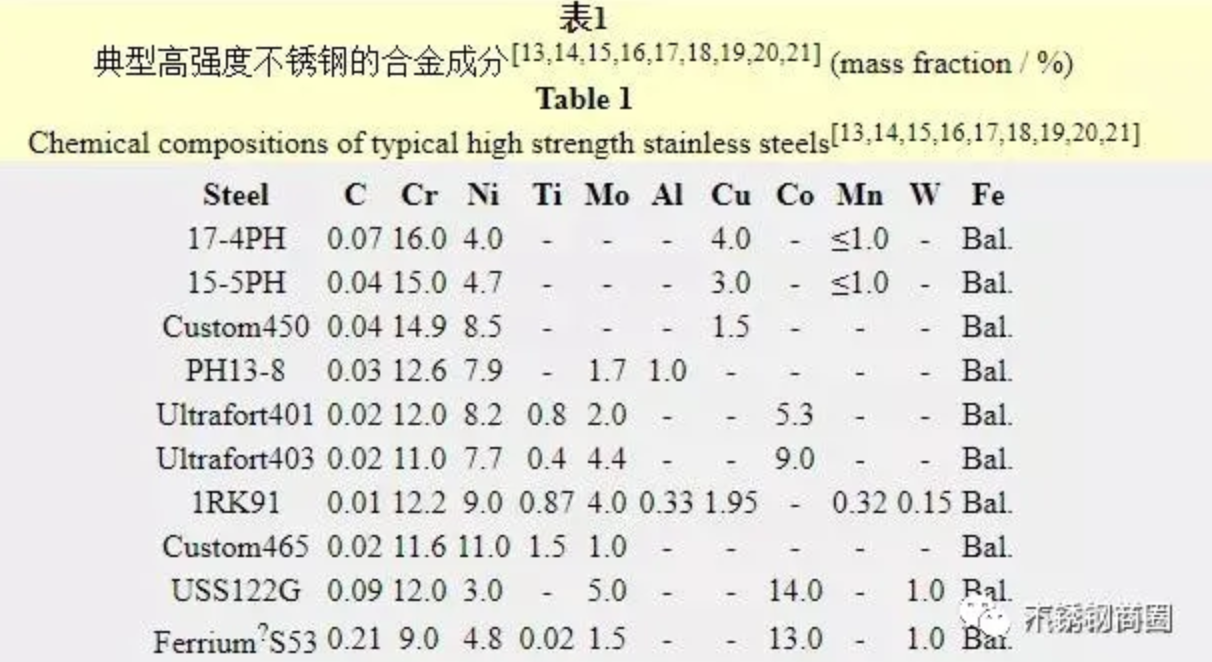
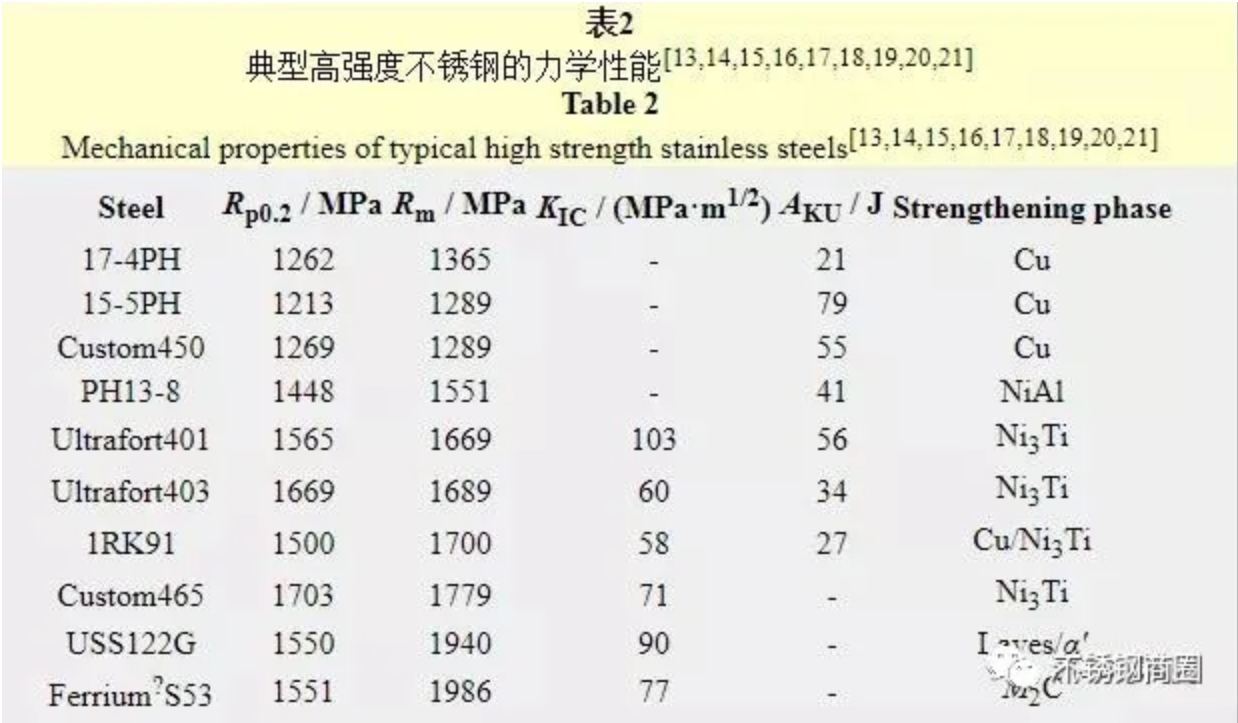
作為第一代高強(qiáng)度不銹鋼的典型代表,15-5PH鋼的合金化特點(diǎn)是采用15%左右的Cr來(lái)保證鋼的耐腐蝕性能;5%左右的Ni含量可以起到平衡實(shí)驗(yàn)用鋼的Cr-Ni當(dāng)量,使鋼在室溫得到馬氏體組織,同時(shí)降低鋼中δ-鐵素體;加入4%左右的Cu,起到了強(qiáng)化作用;少量的Nb可以與C形成MC相,起到了釘扎晶界、細(xì)化晶粒的作用。經(jīng)過(guò)550℃時(shí)效處理后,在馬氏體基體上析出大量fcc結(jié)構(gòu)的富Cu相,富Cu相與馬氏體基體的取向關(guān)系滿足K-S關(guān)系。Habibi-Bajguirani等[22,23]的研究顯示,15-5PH鋼在時(shí)效過(guò)程中存在2種不同類型的Cu的析出相,在低于500℃時(shí)效時(shí),會(huì)首先形成bcc結(jié)構(gòu)的簇狀顆粒,這種簇狀物會(huì)隨后演變?yōu)?/span>9R結(jié)構(gòu),最后轉(zhuǎn)變?yōu)?/span>fcc的沉淀析出相,對(duì)析出相萃取物的X射線微區(qū)分析結(jié)果顯示,這種析出相實(shí)際上是富Cu相。在650~700℃時(shí)效時(shí),fcc的富Cu相一開始與基體保持共格關(guān)系,隨后轉(zhuǎn)變?yōu)榘牍哺竦?/span>K-S關(guān)系。
作為第二代高強(qiáng)度不銹鋼的典型代表,PH13-8Mo采用低碳的合金化設(shè)計(jì),采用13%左右的Cr來(lái)保證鋼的耐蝕性,8%左右的Ni可以彌補(bǔ)由于低碳而引起Schaeffler圖中Cr-Ni當(dāng)量不平衡,降低δ-鐵素體含量,可使鋼得到板條馬氏體組織,加入1%Al可在鋼中形成強(qiáng)化相,起到強(qiáng)化基體的作用[24,25]。Schober等[26]研究了Ti元素對(duì)時(shí)效過(guò)程中析出相演變規(guī)律的影響,結(jié)果表明,在未添加Ti元素的PH13-8Mo鋼中,析出相僅有NiAl相,添加Ti元素后,鋼中的析出相為G相和η相。在時(shí)效處理初期未添加Ti元素的PH13-8Mo鋼中析出的是有序的金屬間化合物NiAl,隨著時(shí)效時(shí)間的延長(zhǎng),NiAl相中的合金元素逐漸趨于化學(xué)計(jì)量平衡并且硬度達(dá)到最大值。在添加Ti元素的鋼中,在時(shí)效處理初期鋼中析出一種富含Ni、Si、Al、Ti的析出相,鋼的硬度在此時(shí)達(dá)到最大值。隨著時(shí)效時(shí)間的延長(zhǎng),鋼中會(huì)形成橢球狀的Ni16Si7Ti6-G相和短桿狀的Ni3(Ti, Al)-η相。
在超高強(qiáng)度不銹鋼的成分設(shè)計(jì)時(shí),為保證鋼具有良好的耐腐蝕性能,一般鋼中Cr的含量應(yīng)大于10%,Cr也是降低馬氏體相變溫度的元素。Ni可以提高不銹鋼的電位和鈍化傾向,增加鋼的耐蝕性能,提高鋼的塑性和韌性,特別是鋼在低溫下的韌性,Ni還會(huì)形成強(qiáng)化作用的η-Ni3Ti相。加入Mo主要是增加了二次硬化效應(yīng),2%左右的Mo可使鋼在不同固溶處理?xiàng)l件下均保持較高的硬度,在時(shí)效過(guò)程中析出的富Mo析出相起到了強(qiáng)化作用,同時(shí)能使鋼保持良好的韌性,Mo還可以提高不銹鋼的耐海水腐蝕性能。Co可以抑制馬氏體中位錯(cuò)亞結(jié)構(gòu)的回復(fù),為析出相的形成提供更多的形核位置,降低Mo在α-Fe中的溶解度,促進(jìn)含Mo的析出相生成,起到了間接強(qiáng)化的作用[25]。另外,在鋼中加入少量的Ti會(huì)明顯提高鋼的強(qiáng)度,但過(guò)量的加入則會(huì)使鋼的韌性下降。Li等[27]研究了一種強(qiáng)度高達(dá)1900 MPa的Cr-Ni-Co-Mo系的馬氏體沉淀硬化不銹鋼,認(rèn)為超高強(qiáng)度的獲得是由于多種強(qiáng)化相復(fù)合強(qiáng)化的結(jié)果。該鋼的名義成分為0.004C-13.5Cr-12.7Co-3.3Mo-4.4Ni-0.5Ti-0.2Al (原子分?jǐn)?shù),%),鋼中的析出相主要有3種,η-Ni3(Ti, Al)相、富Mo的R'相和富Cr的α'相,這些析出相分別是由時(shí)效初期富Ni-Ti-Al、富Mo和富Cr的簇狀顆粒轉(zhuǎn)變而來(lái),時(shí)效過(guò)程中由于富Mo R'相和富Cr α'相的隔離作用使η-Ni3(Ti, Al)相長(zhǎng)大緩慢。
從高強(qiáng)度不銹鋼的發(fā)展來(lái)看,隨著強(qiáng)度級(jí)別的提升,由單一強(qiáng)化相強(qiáng)化逐漸向多相復(fù)合強(qiáng)化發(fā)展,相較于單一種類析出相的強(qiáng)化,復(fù)合強(qiáng)化更有利于鋼強(qiáng)度的進(jìn)一步提升。然而,合金成分和時(shí)效制度對(duì)于不同種類沉淀相的析出和長(zhǎng)大行為的影響差異較大??紤]到不同合金成分和熱處理制度在設(shè)計(jì)新鋼種時(shí)可以獲得不同的多種的沉淀相,采用傳統(tǒng)的試錯(cuò)法實(shí)驗(yàn)和基于數(shù)據(jù)積累的人工神經(jīng)網(wǎng)絡(luò)模擬在合金設(shè)計(jì)過(guò)程中仍存在不足,因此亟需一種新型的基于物理冶金的模型[28]。Xu等[28,29,30]和Parn等[31]提出了一種基于機(jī)器學(xué)習(xí)的合金成分計(jì)算模型,此模型整合了合金成分和相應(yīng)的熱處理參數(shù),實(shí)現(xiàn)了所需的性能在遺傳框架內(nèi)演變。此模型應(yīng)用于設(shè)計(jì)以MC碳化物為強(qiáng)化相的超高強(qiáng)度鋼,亦適用于Cu團(tuán)簇、Ni3Ti、NiAl沉淀相,也可應(yīng)用于設(shè)計(jì)一種由多種類強(qiáng)化相,包括MC碳化物、富Cu相和Ni3Ti金屬間化合物共同強(qiáng)化合金。模型包括了對(duì)鋼力學(xué)性能、耐蝕性能以及顯微組織等相應(yīng)參數(shù)的模擬,為合金的成分設(shè)計(jì)提供了更為可靠的路徑。
2.2 高強(qiáng)度不銹鋼中的韌化相及韌化機(jī)理逆轉(zhuǎn)變奧氏體對(duì)高強(qiáng)度不銹鋼韌性的影響與其形貌、含量、彌散度和穩(wěn)定性等有緊密的關(guān)系,其特征又受到熱處理過(guò)程的加熱速率、等溫溫度和時(shí)間、奧氏體形成元素的擴(kuò)散和偏析、奧氏體的形核位置、尺寸以及基體內(nèi)部位錯(cuò)密度的影響?,F(xiàn)有研究表明,逆轉(zhuǎn)變奧氏體的形成機(jī)制有如下3種,即無(wú)擴(kuò)散切變逆轉(zhuǎn)變機(jī)制[32]、變體限制機(jī)制[33]以及殘余奧氏體長(zhǎng)大機(jī)制[34]。切變機(jī)制源于奧氏體向馬氏體的無(wú)擴(kuò)散切變機(jī)制的逆過(guò)程,與原奧氏體保持一定晶體學(xué)位相關(guān)系的馬氏體形成的逆轉(zhuǎn)變奧氏體,與原奧氏體保持相同的位相關(guān)系。變體限制機(jī)制則指出,由擴(kuò)散控制的逆轉(zhuǎn)變奧氏體形成過(guò)程中,其形核位置將與原奧氏體、碳化物及基體嚴(yán)格保持一定的晶體學(xué)位相關(guān)系,因此限制了逆轉(zhuǎn)變奧氏體的變體種類。而殘余奧氏體長(zhǎng)大機(jī)制則認(rèn)為,馬氏體鋼中淬火后殘留下的奧氏體會(huì)在其后的回火過(guò)程中通過(guò)奧氏體穩(wěn)定元素的擴(kuò)散不斷長(zhǎng)大,從而進(jìn)一步“逆轉(zhuǎn)變”為新的奧氏體組織。對(duì)0Cr13Ni4Mo馬氏體不銹鋼的研究[34]顯示,在稍高于奧氏體轉(zhuǎn)變開始溫度(AS)的兩相區(qū)回火時(shí),碳化物(Cr23C6)和奧氏體共同析出。進(jìn)一步分析碳化物和奧氏體及其界面上的Cr、Ni元素分布情況,發(fā)現(xiàn)Cr在碳化物中的偏聚促進(jìn)了Ni元素向逆轉(zhuǎn)變奧氏體中的配分,Ni元素的富集降低了逆轉(zhuǎn)變奧氏體形成的化學(xué)驅(qū)動(dòng)力并增加了界面能,因此,富Ni區(qū)域可作為逆轉(zhuǎn)變奧氏體在回火過(guò)程中的形核點(diǎn)位,即逆轉(zhuǎn)變奧氏體的形成受到Ni元素?cái)U(kuò)散的控制。進(jìn)一步提高回火溫度,雖然原子的擴(kuò)散更為顯著,但是由于溫度的提高,回火馬氏體向奧氏體的轉(zhuǎn)變驅(qū)動(dòng)力條件已得到滿足,故此時(shí)的逆轉(zhuǎn)變奧氏體形成機(jī)制為無(wú)擴(kuò)散的切變機(jī)制。為了進(jìn)一步說(shuō)明變體限制機(jī)制,Nakada等[35]研究了逆轉(zhuǎn)變奧氏體同原奧氏體及馬氏體基體的晶體學(xué)位相關(guān)系。13Cr-6Ni鋼回火后,一個(gè)原奧晶粒內(nèi),逆轉(zhuǎn)變奧氏體不僅均勻分布于馬氏體板條界,其同位相束(blocks)和板條群(packets)界面處亦存在逆轉(zhuǎn)變奧氏體,并且大部分與原奧保持相同取向,而少部分取向與原奧氏體不同。一個(gè)原奧氏體慣習(xí)面和一個(gè)馬氏體板條群中可能存在12種逆轉(zhuǎn)變奧氏體變體的位相關(guān)系。可以看到,在遵循K-S關(guān)系的前提下,只存在與密排面平行的6種不同方向的馬氏體板條束,每一種馬氏體板條束內(nèi)部只存在2種逆轉(zhuǎn)變奧氏體變體。這說(shuō)明由于奧氏體在{111}γ晶面族的三重對(duì)稱性,一個(gè)馬氏體板條群中的12種逆轉(zhuǎn)變奧氏體變體可被分為2類,即與原奧保持相同取向的V1變體和與V1具有孿生關(guān)系的V2變體。根據(jù)Lee和Aaronson提出的二維構(gòu)建模型[35],逆轉(zhuǎn)變奧氏體的臨界晶核形狀應(yīng)當(dāng)滿足最小化形核能的要求。在板條界面處形成的逆轉(zhuǎn)變奧氏體通常與原奧氏體晶粒的取向一致,其核心的α'/γ界面與馬氏體基體兩側(cè)均保持K-S關(guān)系,而原奧晶界處的奧氏體核心只與一側(cè)的基體保持了K-S關(guān)系。因此,原奧晶界處的逆轉(zhuǎn)變奧氏體由于被共格和非共格界面包裹,及兩側(cè)界處表面能和彈性應(yīng)變能的差異,會(huì)形成圓球狀的形貌,而位于板條界的逆轉(zhuǎn)變奧氏體則傾向于形成長(zhǎng)條針狀形貌。
逆轉(zhuǎn)變奧氏體含量的增加可以提高材料的塑性和韌性,而過(guò)多的逆轉(zhuǎn)變奧氏體往往會(huì)導(dǎo)致鋼屈服強(qiáng)度的惡化。Schnitzer等[36]分別計(jì)算了PH13-8Mo中強(qiáng)化相NiAl和韌化相逆轉(zhuǎn)變奧氏體對(duì)整體屈服強(qiáng)度的影響,時(shí)效處理后屈服強(qiáng)度40%的降低量歸因于高含量的逆轉(zhuǎn)變奧氏體,其余則歸于NiAl相的粗化。因此在要求高韌性的情況,應(yīng)采用較高的時(shí)效溫度使逆轉(zhuǎn)變奧氏體含量提高[37],但需以損失材料的強(qiáng)度為代價(jià)。另外,一些研究中也發(fā)現(xiàn)逆轉(zhuǎn)變奧氏體對(duì)塑性的不利作用,如Viswanathan等[38]的結(jié)果表明,逆轉(zhuǎn)變奧氏體對(duì)塑性的提高僅在時(shí)效初期出現(xiàn),時(shí)間延長(zhǎng)同樣會(huì)使材料發(fā)生嚴(yán)重的脆性斷裂。
2.3 高強(qiáng)度不銹鋼的氫脆敏感性和應(yīng)力腐蝕研究隨著強(qiáng)度級(jí)別的升高,高強(qiáng)度鋼對(duì)應(yīng)力腐蝕開裂(stress corrosioncracking,SCC)和氫脆(hydrogenembrittlement,HE)亦越發(fā)敏感。尤其,當(dāng)污染性或腐蝕性氣體組分及H原子與應(yīng)力聯(lián)合作用于高強(qiáng)度鋼時(shí),極易導(dǎo)致裂紋萌生并逐漸擴(kuò)展直至開裂。此種斷裂是服役于腐蝕環(huán)境中的高強(qiáng)度鋼結(jié)構(gòu)件的主要失效形式,造成了巨大的安全隱患和財(cái)產(chǎn)損失。
可擴(kuò)散氫是造成鋼塑性損失的主要因素[39],任何降低可擴(kuò)散氫的移動(dòng)性的措施均可有效提高材料的氫脆敏感抗力。強(qiáng)氫陷阱可顯著增加鋼吸收過(guò)飽和氫的含量,從而使得進(jìn)入基體中的氫無(wú)害化。上述觀點(diǎn)在觀察高強(qiáng)鋼的氫致延遲斷裂的現(xiàn)象中得到了一定程度的證實(shí),即當(dāng)高強(qiáng)鋼在低于其抗拉強(qiáng)度的靜態(tài)應(yīng)力作用下,其會(huì)在服役一段時(shí)間發(fā)生瞬時(shí)脆斷,這種在靜載荷下發(fā)生的失效是由于侵入基體的H原子造成的[40]。作為鋼中最主要的強(qiáng)化相和韌化相,時(shí)效過(guò)程析出的大量彌散分布的第二相強(qiáng)化粒子和逆轉(zhuǎn)變奧氏體均可視為鋼中重要的氫陷阱。大量研究聚焦于通過(guò)熱處理工藝調(diào)控鋼中的“良性氫陷阱”(benign hydrogen traps)的數(shù)量及密度來(lái)阻止H在材料中的擴(kuò)散,從而提高材料的氫脆敏感抗力。大量研究顯示碳化物是鋼中典型的“良性氫陷阱”并可以有效提高鋼的氫脆敏感性。例如,通過(guò)球化滲碳體顆粒或通過(guò)在奧氏體單相區(qū)內(nèi)成形冷卻后快速加熱到回火溫度細(xì)化滲碳體,可有效提高鋼的氫脆敏感抗力[41]。此外,通過(guò)添加Ti、V、Nb等微合金化元素,在鋼中形成了TiC、VC、NbC等碳化物,均可作為有效的氫陷阱[42,46]。Takahashi等[47,48]利用APT直接觀察到了TiC和V4C3陷阱捕獲了氘原子。H主要被捕獲于TiC和基體的界面上,而V4C3中的陷阱點(diǎn)位主要是半共格界面上錯(cuò)配位錯(cuò)(misfit dislocation)芯部位置。借助第一性原理計(jì)算和有限元分析,進(jìn)一步證實(shí)對(duì)于TiC析出而言,TiC-基體界面是主要的氫陷阱,而碳空位是V4C3中的主要陷阱位點(diǎn)[49]。
金屬間化合物及元素富集相作為氫陷阱的研究則鮮有報(bào)道。近期,Li等[50]對(duì)比了蒸汽輪機(jī)末級(jí)葉片用17-4PH鋼和PH13-8Mo鋼的氫脆行為,其研究結(jié)果表明,鋼中析出相的類型以及馬氏體基體與析出相的晶體學(xué)關(guān)系,是導(dǎo)致PH13-8Mo鋼相較17-4PH鋼具有更高的表觀氫擴(kuò)散系數(shù)和更低的表觀氫溶解度的主要原因。17-4PH鋼中存在與基體非共格的富Cu相,相較于PH13-8Mo鋼中的共格β-NiAl相,其對(duì)H原子具有更強(qiáng)的捕獲能力。這是因?yàn)楦籆u相的八面體間隙的半徑為0.0529 nm,約為β-NiAl相八面體間隙的半徑(0.0206 nm)的2倍。而且,同β-NiAl相與基體的共格界面相比,富Cu相與基體的非共格界面可捕獲更多H原子。此外,共格界面上錯(cuò)配位錯(cuò)的芯部和臨近芯部的畸變程度較小的晶格均為弱氫陷阱[51,52],且非共格析出相的氫脫附能(de-trapping energy)高于共格析出相的脫附能[53]。
與馬氏體基體相比,H在殘余(或逆轉(zhuǎn)變)奧氏體的擴(kuò)散速率更低(在奧氏體中的擴(kuò)散速率:10-15~10-16 m2/s,在馬氏體中的擴(kuò)散速率:10-10~10-12 m2/s),且H在奧氏體中的溶解度相較馬氏體更高。此外,奧氏體對(duì)于H的釘扎能可達(dá)55 kJ/mol[54],使其可作為不可逆H陷阱位點(diǎn)。然而,對(duì)于不同體系鋼中奧氏體相對(duì)于材料的氫脆敏感性的影響仍存在廣泛的爭(zhēng)議。一些結(jié)果[55,56]表明,鋼中的逆轉(zhuǎn)變奧氏體和細(xì)小的殘余奧氏體可有效阻止H在基體中的擴(kuò)散,從而提高了鋼的氫脆敏感抗力。與此相反,亦有學(xué)者[57,58]指出固溶進(jìn)入奧氏體中的H原子可降低其層錯(cuò)能,使得TRIP效應(yīng)更易發(fā)生,新生馬氏體作為“氫源”會(huì)釋放出H原子,從而造成材料的脆化[59]。Fan等[60]報(bào)道了逆轉(zhuǎn)變奧氏體對(duì)于S41500馬氏體不銹鋼(名義成分為0.04C-13Cr-4.1Ni-0.6Mo-0.7Mn,%)的氫脆斷裂行為的影響,H原子主要富集于富Ni的逆轉(zhuǎn)變奧氏體中,而奧氏體/馬氏體界面及奧氏體/碳化物界面處無(wú)H原子的富集?;鼗鹛幚砗笤嚇訙?zhǔn)解理斷口的TEM觀察結(jié)果顯示,斷裂路徑是沿著回火馬氏體和發(fā)生相變誘導(dǎo)塑性(TRIP)效應(yīng)新生成的馬氏體(NFM)的界面,這是因?yàn)榇蟛糠值腍已被逆轉(zhuǎn)變奧氏體捕獲,而非偏聚在原奧晶界處,從而降低了逆轉(zhuǎn)變奧氏體的穩(wěn)定性,促進(jìn)了馬氏體相變。相變發(fā)生后,新生馬氏體將作為氫源釋放大量的H原子,使得其周圍界面聚集了大量的H原子,所產(chǎn)生的斷口形貌為準(zhǔn)解理形貌而非沿晶斷裂形貌。
氫致裂紋一般于板條、同位相束、板條群及原奧晶界處形核,而后裂紋在外應(yīng)力的作用下穿過(guò)板條束,沿著板條群和原奧晶界擴(kuò)展。高強(qiáng)度不銹鋼中眾多馬氏體多級(jí)組織界面(原奧氏體晶界、馬氏體板條群界、馬氏體板條束界及馬氏體板條界)以及相界是高強(qiáng)度不銹鋼具有較高氫脆敏感性的原因之一。對(duì)17-4PH鋼中氫的擴(kuò)散和氫脆行為的研究結(jié)果顯示,固溶態(tài)試樣的氫脆敏感抗力高于峰時(shí)效態(tài)試樣,此現(xiàn)象主要是因?yàn)樵跁r(shí)效態(tài)試樣中富Cu相和基體的相界面相捕獲了較多的H,界面結(jié)合力的弱化造成了峰時(shí)效態(tài)充氫試樣的脆斷。隨著固溶處理溫度的升高,17-4PH鋼的氫脆敏感性和氫的擴(kuò)散系數(shù)均呈先上升后下降的趨勢(shì)。這主要?dú)w因于固溶溫度對(duì)于鋼中原奧氏體晶界和其后時(shí)效處理過(guò)程中析出相的數(shù)密度的影響,伴隨著固溶溫度的升高,原奧晶粒變大、晶界面積減小,但基體對(duì)于Cu原子的固溶度增加,促進(jìn)了時(shí)效過(guò)程中富Cu相的析出,而析出相密度及尺寸的增加提供了更多的相界面,二者共同提供了可捕獲H的界面。
顯然,高強(qiáng)度不銹鋼的氫脆敏感性是由鋼中復(fù)雜多級(jí)及多相組織共同決定的,由于分析表征手段的限制,仍很難定量確定各類氫陷阱對(duì)于高強(qiáng)度不銹鋼的氫脆敏感性的影響?;诓煌瑥?qiáng)度級(jí)別、利用不同強(qiáng)化體系強(qiáng)化的高強(qiáng)度不銹鋼的氫脆敏感性影響因素仍待系統(tǒng)而深入的研究。具有復(fù)雜合金體系、多相耦合強(qiáng)化的超高強(qiáng)度不銹鋼的氫脆敏感性更是亟待研究。目前,筆者團(tuán)隊(duì)研發(fā)了一種由多相復(fù)合析出強(qiáng)化的新型2200 MPa級(jí)高強(qiáng)度不銹鋼,該實(shí)驗(yàn)用鋼的名義成分為0.2C-9Cr-4.2Ni-3.1Mo-15.2Co-0.3V-0.9W(%),其雙時(shí)效態(tài)試樣的APT分析結(jié)果如圖1所示。由圖可見(jiàn),鋼中存在明顯的富Mo/Cr/C、Mo/Cr及單純的富Cr團(tuán)簇,進(jìn)一步分析可知鋼中的析出相包括金屬間化合物、碳化物及富Cr相,其超高強(qiáng)度是由3種析出相耦合強(qiáng)化獲得的,亦是目前已報(bào)道的強(qiáng)度級(jí)別最高的高強(qiáng)度不銹鋼。筆者團(tuán)隊(duì)亦在進(jìn)行該鋼種的氫脆敏感抗力的相關(guān)研究,以期揭示不同種類析出相耦合強(qiáng)化高強(qiáng)度不銹鋼中不同種類氫陷阱共同作用對(duì)其氫脆敏感抗力的影響,為提高2200 MPa級(jí)超高強(qiáng)度不銹鋼的綜合服役性能提供理論依據(jù)。
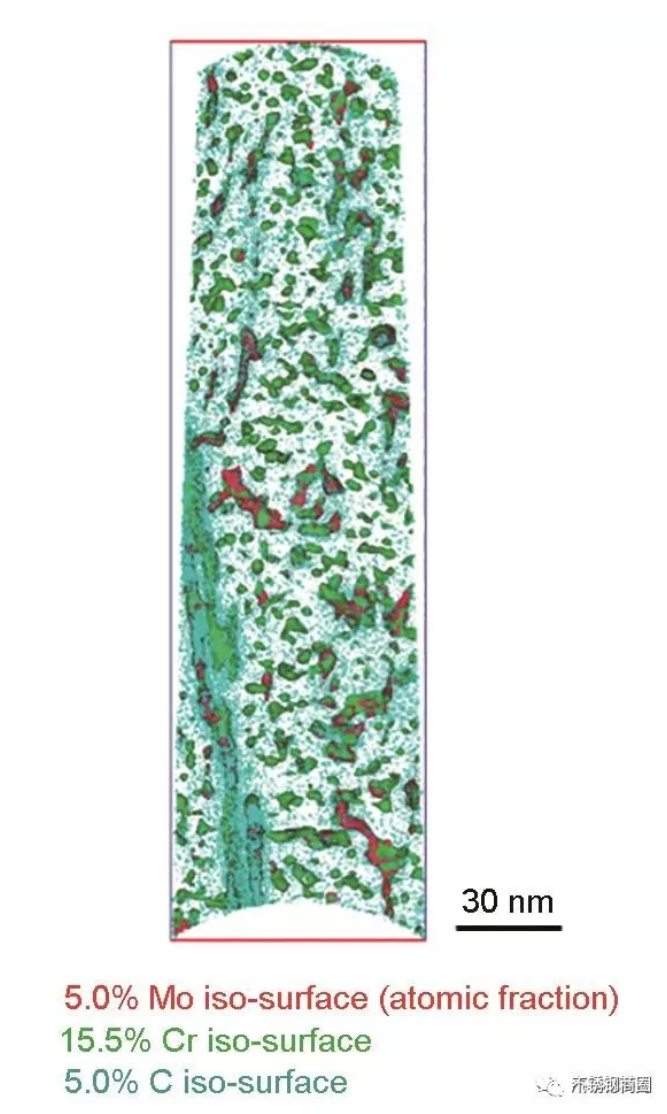
圖1 新型高強(qiáng)度不銹鋼時(shí)效態(tài)試樣APT表征結(jié)果
Fig.1 Atom probe tomography (APT) map within a selectedcube (box size is 70 nm×70 nm×240 nm) of a newly developed ultra-high strengthsteel aged specimen
美國(guó)飛機(jī)部件破壞調(diào)查報(bào)告顯示,應(yīng)力腐蝕開裂是飛機(jī)關(guān)鍵承力部件在服役過(guò)程中發(fā)生突發(fā)性破壞事故的主要形式之一,起落架多數(shù)是由于應(yīng)力腐蝕或疲勞裂紋擴(kuò)展而導(dǎo)致最后斷裂[61]。目前,不僅是在航空、航天、能源、化工等高新技術(shù)和產(chǎn)業(yè),在幾乎所有常用的耐腐蝕鋼種和合金中都會(huì)發(fā)生應(yīng)力腐蝕現(xiàn)象。因此,分析超高強(qiáng)度鋼應(yīng)力腐蝕開裂機(jī)理,并對(duì)影響超高強(qiáng)度鋼的應(yīng)力腐蝕的因素進(jìn)行分析,對(duì)確定超高強(qiáng)度鋼應(yīng)力腐蝕防護(hù)措施具有重大的科學(xué)價(jià)值和現(xiàn)實(shí)意義。
材料的耐蝕性能成為限制高強(qiáng)度鋼應(yīng)力腐蝕開裂的重要因素,而點(diǎn)蝕是最為常見(jiàn)也是危害最大的腐蝕形式。多數(shù)應(yīng)力腐蝕開裂均起源于點(diǎn)蝕坑,超高強(qiáng)度不銹鋼由于時(shí)效處理過(guò)程中,從過(guò)飽和馬氏體基體中脫溶的析出相造成了顯微組織的不均勻性,是超高強(qiáng)度不銹鋼發(fā)生點(diǎn)蝕的主要根源。析出相附近鈍化膜比較薄弱,Cl-的侵入引起鈍化膜的破壞,析出相和基體之間形成微電池,從而使基體溶解,析出相剝落,形成點(diǎn)蝕。例如,富Cr型的碳化物M23C6、M6C和金屬間化合物L(fēng)aves相和σ相等周圍易形成貧Cr區(qū),造成點(diǎn)蝕現(xiàn)象的發(fā)生。Luo等[62]和余強(qiáng)[63]利用三維原子探針層析技術(shù)研究了時(shí)效時(shí)間對(duì)15-5PH超高強(qiáng)度不銹鋼組織和電化學(xué)行為的影響,在時(shí)效時(shí)間為1~240 min時(shí)觀察到了富含Cu的團(tuán)簇和(Cu, Nb)的納米顆粒,與短期時(shí)效處理相比,長(zhǎng)期時(shí)效處理后的樣品表面更容易受到Cl-的侵蝕。在時(shí)效240 min后,析出物周圍的Cr含量也會(huì)下降,這些部位易形成貧Cr區(qū)。而鈍化膜中Cr/Fe比值的降低是導(dǎo)致鈍化膜耐點(diǎn)蝕性能下降的原因。除此之外,富Cr型碳化物在晶界上的連續(xù)析出會(huì)降低鋼的耐晶間腐蝕性能。例如,研究[64]發(fā)現(xiàn),AISI 316Ti不銹鋼比AISI 321不銹鋼具有更高的抗晶間腐蝕性能,究其原因是由于TiC的析出減少了富Cr型碳化物的形成,而富Cr碳化物是導(dǎo)致晶間腐蝕的析出物之一。
作為高強(qiáng)度不銹鋼中最主要的韌性相,奧氏體的含量、形貌、尺寸及穩(wěn)定性同樣會(huì)影響鋼的應(yīng)力腐蝕敏感性。在尺寸、形貌及穩(wěn)定性相同的情況下,隨著奧氏體含量的增加,應(yīng)力腐蝕開裂門檻值(KISCC)增大,鋼的應(yīng)力腐蝕開裂敏感性降低。究其原因,是因?yàn)轳R氏體板條界上形成的薄膜狀?yuàn)W氏體組織提高了鋼的韌性,降低了氫致裂紋的擴(kuò)展速率,造成裂紋擴(kuò)展速率降低的主要原因有2點(diǎn),其一:裂紋由馬氏體基體擴(kuò)展至薄膜狀的奧氏體時(shí),無(wú)論是繼續(xù)擴(kuò)展進(jìn)入奧氏體內(nèi)部或是改變擴(kuò)展方向繞過(guò)奧氏體組織,均會(huì)消耗較大的能量,導(dǎo)致裂紋的擴(kuò)展速率降低,抗應(yīng)力腐蝕敏感性提高;其二:如前所述,H在奧氏體組織中有較高的固溶度,較低的偏聚傾向,且H在奧氏體中的擴(kuò)散速率遠(yuǎn)比在馬氏體組織中的小,是高強(qiáng)度不銹鋼中有益的氫陷阱,導(dǎo)致裂紋前端的氫脆敏感性降低,進(jìn)而裂紋的擴(kuò)展速率降低,應(yīng)力腐蝕敏感性提高。需要說(shuō)明的是,奧氏體的穩(wěn)定性同樣是決定鋼應(yīng)力腐蝕敏感性的關(guān)鍵參數(shù),應(yīng)力或應(yīng)變誘導(dǎo)發(fā)生馬氏體相變后,由奧氏體轉(zhuǎn)變的新鮮馬氏體非但不能抑制裂紋的擴(kuò)展,還會(huì)作為新的氫擴(kuò)散源導(dǎo)致鋼氫脆敏感提高。
綜上所述,鋼的強(qiáng)韌性、應(yīng)力腐蝕及氫脆敏感性均受到復(fù)雜多級(jí)多相組織的影響,而采用傳統(tǒng)試錯(cuò)法設(shè)計(jì)和制備兼具超高強(qiáng)韌性及優(yōu)良服役性能的超高強(qiáng)度不銹鋼難度大、周期長(zhǎng)、成本高。相比于試錯(cuò)法,理性的設(shè)計(jì)方法,例如通過(guò)建立“原子尺寸-納米尺度-微米尺度”等一系列多尺度的強(qiáng)韌性、應(yīng)力腐蝕性能及氫脆性能分析模型,將更具有目的性。通過(guò)模擬分析結(jié)果建立高強(qiáng)度不銹鋼的設(shè)計(jì)標(biāo)準(zhǔn),優(yōu)化鋼中析出相、馬氏體及奧氏體組織的形態(tài)、尺寸及含量等,進(jìn)一步將多尺度模擬和實(shí)際材料研發(fā)過(guò)程相結(jié)合,將大大降低材料研發(fā)難度,減少成本投入并縮短研發(fā)周期。
作為兼?zhèn)鋬?yōu)良強(qiáng)韌性及服役安全性的金屬結(jié)構(gòu)材料,高強(qiáng)度不銹鋼在未來(lái)的航空、航天、海洋工程及核工業(yè)等領(lǐng)域有著廣闊的應(yīng)用前景。鑒于此類鋼種苛刻的應(yīng)用環(huán)境,對(duì)新一代高強(qiáng)度不銹鋼的探索除了著眼于進(jìn)一步突破超高強(qiáng)度-優(yōu)良塑韌性匹配的瓶頸,還應(yīng)該兼顧優(yōu)良的服役安全性。在合金設(shè)計(jì)和熱處理工藝制定過(guò)程中,由傳統(tǒng)的試錯(cuò)法逐漸過(guò)渡到熱/動(dòng)力學(xué)輔助合金設(shè)計(jì)、人工智能機(jī)械學(xué)習(xí)等理性設(shè)計(jì)方法,以極大提高新型高強(qiáng)度耐蝕合金的研發(fā)周期、節(jié)約研發(fā)成本;對(duì)于高強(qiáng)度不銹鋼中強(qiáng)韌化機(jī)理的研究仍待進(jìn)一步深入,尤其是對(duì)多相復(fù)合強(qiáng)化第二相粒子的析出行為的理解及強(qiáng)化貢獻(xiàn)值的疊加;對(duì)于鋼中奧氏體含量、尺寸、形貌及穩(wěn)定性對(duì)高強(qiáng)度不銹鋼韌性影響的研究較為充分,但仍未建立有效的數(shù)學(xué)模型定量估算其對(duì)于該鋼種韌性的貢獻(xiàn)量;此外,對(duì)于超高強(qiáng)度級(jí)別高強(qiáng)度不銹鋼復(fù)雜強(qiáng)化體系下的應(yīng)力腐蝕斷裂機(jī)理和氫脆敏感性的研究亟待解決,從而為超高強(qiáng)度級(jí)別高強(qiáng)度不銹鋼的耐久性設(shè)計(jì)提供可以借鑒的理論依據(jù)。 (作者:劉振寶, 梁劍雄, 蘇杰, 王曉輝, 孫永慶, 王長(zhǎng)軍, 楊志勇(鋼鐵研究總院特殊鋼研究所)